北京塑料模具企业
医疗器械注塑模具的加工难点是什么?小批量生产医疗器械的生产往往是小批量的,这就要求注塑模具的设计和加工必须具有很高的灵活性和适应性。一方面,需要能够快速响应客户需求的变化,另一方面,需要能够在大批量生产和小批量生产之间灵活切换,以满足市场的多样化需求。综上所述,医疗器械注塑模具的加工难点主要体现在高精度要求、复杂的形状和结构、高耐磨性和耐腐蚀性、严格的质量控制、长寿命要求以及小批量生产等方面。为了克服这些难点,需要不断提高加工设备和技术水平,加强操作人员的培训和管理,同时积极引进和应用先进的加工技术和方法,以确保医疗器械注塑模具的加工质量和效率得到不断提高。塑胶模具的作用是实现塑料制品的量产,满足市场需求,推动经济发展。北京塑料模具企业
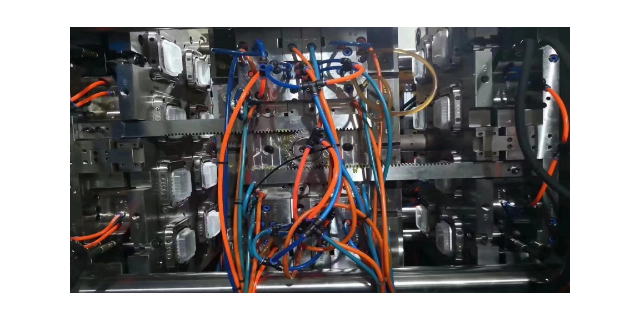
车灯注塑模具的制造材料一般会选择以下几种:1. 钢材:钢材是注塑模具常用的材料之一,具有强度高、耐腐蚀、耐磨等特点。2. 铝合金:铝合金具有重量轻、易加工、耐腐蚀等特点,是注塑模具的常用材料之一。3. 铜合金:铜合金具有高导热性、高精度等特点,常用于制造注塑模具的镶件和细小部件。4. 耐磨材料:耐磨材料如硬质合金、陶瓷等可以用于制造注塑模具的关键部位,如型芯、型腔等,提高模具的耐磨性和寿命。5. 其他材料:其他材料如合成树脂、增强纤维等也可以用于制造注塑模具。血糖仪塑料模具哪家便宜手工调试和校验是制作电子吸塑模具的重要步骤,确保模具的精度和稳定性。
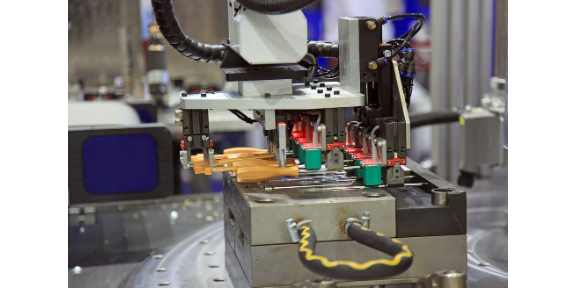
如何提高塑胶模具的耐磨性?如何提高塑胶模具的耐磨性塑胶模具是一种普遍应用于工业生产中的关键工具,其耐磨性能直接影响到产品的质量和生产效率。随着工业技术的不断进步,塑胶模具的耐磨性成为了制造业关注的焦点。这里将探讨提高塑胶模具耐磨性的几种方法,包括材料选择、表面处理和制造工艺等方面的改进。选择合适的模具材料模具材料的选择是提高耐磨性的关键。好的的模具材料应具有强度高、高硬度、良好的耐磨性和耐腐蚀性。常用的塑胶模具材料有P20、718、S136等。其中,S136具有优异的耐腐蚀性、耐磨性和抛光性能,适用于生产高精度、高表面质量的塑胶产品。
医疗器械注塑模具的加工难点是什么?严格的质量控制医疗器械作为直接关系到人们生命健康的产品,其质量控制是非常严格的。这就意味着注塑模具的质量控制必须非常严格。从原材料的选择、加工工艺的制定、加工过程的监控到成品的检验,每一个环节都需要严格控制,确保较终产品的质量和性能符合要求。长寿命要求由于医疗器械的使用寿命往往较长,这就要求注塑模具具有相应的长寿命。在设计和加工过程中,需要充分考虑到模具的耐磨性、耐疲劳性以及维修性等因素,以确保其在使用过程中能够保持稳定的性能和精度。电子吸塑模具制造过程需要严格遵守相关技术和安全标准。
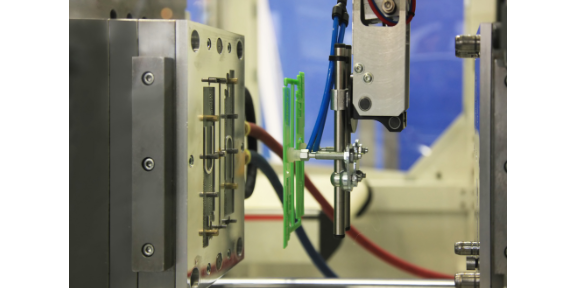
车灯注塑模具在汽车制造过程中扮演着非常重要的角色。汽车车灯是汽车的重要组成部分,主要起到照明、信号传递和装饰车辆的作用。而车灯注塑模具则是制造车灯零件的必要工具。车灯注塑模具是一种精密的模具,通过注塑成型工艺将塑料原料注入到模具型腔中,形成车灯需要的各种形状和尺寸的零件。模具的精度和表面质量直接影响到车灯零件的品质,因此对模具的设计和制造要求非常高。在汽车制造过程中,车灯注塑模具的主要作用是制造车灯的外壳、内部结构、配光镜等零件。这些零件不只需要具有足够的强度和耐久性,同时还要求具有很高的尺寸精度和表面质量。车灯注塑模具的设计和制造需要考虑到许多因素,如材料、注塑工艺、模具材料、冷却系统等。塑胶模具制造的塑料制品具有良好的表面光滑度和一致性,提升产品质量。灯具塑料模具定制厂家
随着科技的进步和创新,电子吸塑模具的设计和制造正朝着智能化的方向发展进步。北京塑料模具企业
车灯注塑模具的冷却和加热过程是注塑成型的关键环节。冷却过程主要发生在注塑成型后,模具被加热到一定温度后,将塑料注入模具。然后,模具被冷却到适当温度以固定塑料制品的形状。一般来说,冷却时间约占整个成型周期的2/3。为了提高生产效率,通常会使用冷却水道或冷却介质来加快模具的冷却速度。在车灯注塑模具中,冷却管道通常被设计在模具的内部,通过在模具内部循环的冷却水来带走热量,使模具尽快冷却到可取出塑料制品的温度。加热过程主要发生在注塑成型前,模具被加热到适当的温度以提高塑料的流动性。加热通常通过电热元件或热介质来实现。在车灯注塑模具中,电热元件可以嵌入模具内部,通电后产生热量,将模具加热到适当的温度。同时,有些模具也会使用热介质(如蒸汽)进行加热。为了确保冷却和加热的均匀性,避免模具局部过热或过冷,影响塑料制品的质量和生产效率,通常会对模具进行分区控制。根据模具的大小和形状,可以分为多个区域,每个区域单独控制加热和冷却。同时,还会使用传感器实时监测模具的温度,以便进行精确的温度控制。北京塑料模具企业
上一篇: 北京专业塑胶模具厂家
下一篇: 北京模具哪家划算